What is soft start? Practical application of soft starter
Strong engine starting and voltage drops affecting the electrical system are problems many businesses encounter, especially in industries using high-capacity engines. Soft start is a solution to help overcome this situation, but is it really suitable for user needs? Understanding the concept, structure and operating principles will help you make better decisions, all in the article below.
Contents
Definition of soft start
Soft starter is a solution that helps control the electric motor starting process, reduces sudden starting current and limits impact on the electrical system. This device is especially suitable for engines with medium and large capacity, helping to operate smoothly and prolong equipment life. Instead of activating immediately with high current, soft starters gradually adjust the voltage and current, ensuring the motor reaches a stable operating state without causing electric shock.
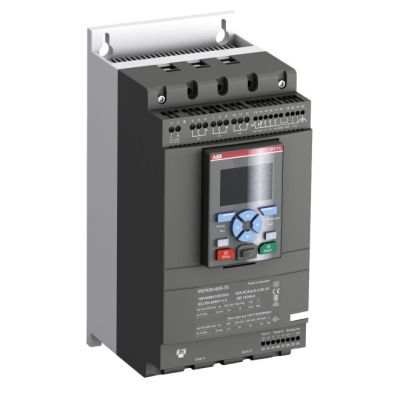
Configure and start the application
Structure
A soft starter consists of the following main components:
Control Unit: Can be either digital, featuring a display and keypad, or mechanical, using potentiometers or rotary switches for adjustments. It includes built-in protection functions such as overload and overheat protection, along with communication protocols like Modbus and Profibus.
Thyristor (SCR - Silicon Control Rectifier): Responsible for controlling and switching the electrical current, regulating the input voltage.
Cooling System and Fan: Ensures stable operation by preventing overheating.
Bypass Contactor: May or may not be integrated, depending on the type of soft starter. Once the motor reaches its rated speed, this contactor closes, allowing direct power supply from the grid to the motor.
Protective Enclosure: Designed according to standards suited for the operating environment, protecting the device from dust, moisture, and mechanical impact.
Principle of operation
A soft starter utilizes three pairs of thyristors (SCRs) connected in parallel and in opposite directions to regulate the voltage supplied to the motor.
When no voltage is applied, the thyristors completely block the electrical current.
During startup, the thyristors gradually open their firing angle (the conduction angle of the semiconductor switches), allowing current to pass through progressively. This enables a smooth motor start, preventing electrical shocks and sudden torque surges.
As the voltage gradually increases to its rated value, the motor reaches its maximum speed.
The bypass contactor then closes, directly connecting the motor to the power grid, reducing losses on the thyristors and optimizing operational efficiency.
Advantages and Applications of Soft Start
A soft starter consists of three pairs of thyristors (SCRs) arranged in parallel and in opposite polarity to control the voltage supplied to the motor.
When no voltage is applied, the thyristors remain fully closed, blocking any current flow.
During startup, the thyristors gradually increase their conduction angle, allowing current to flow progressively. This controlled ramp-up ensures a smooth motor startup, minimizing electrical surges and sudden torque spikes.
As the voltage steadily rises to its nominal level, the motor accelerates to its full operating speed.
At this point, the bypass contactor engages, establishing a direct connection between the motor and the power supply, reducing losses in the thyristors and enhancing overall efficiency.